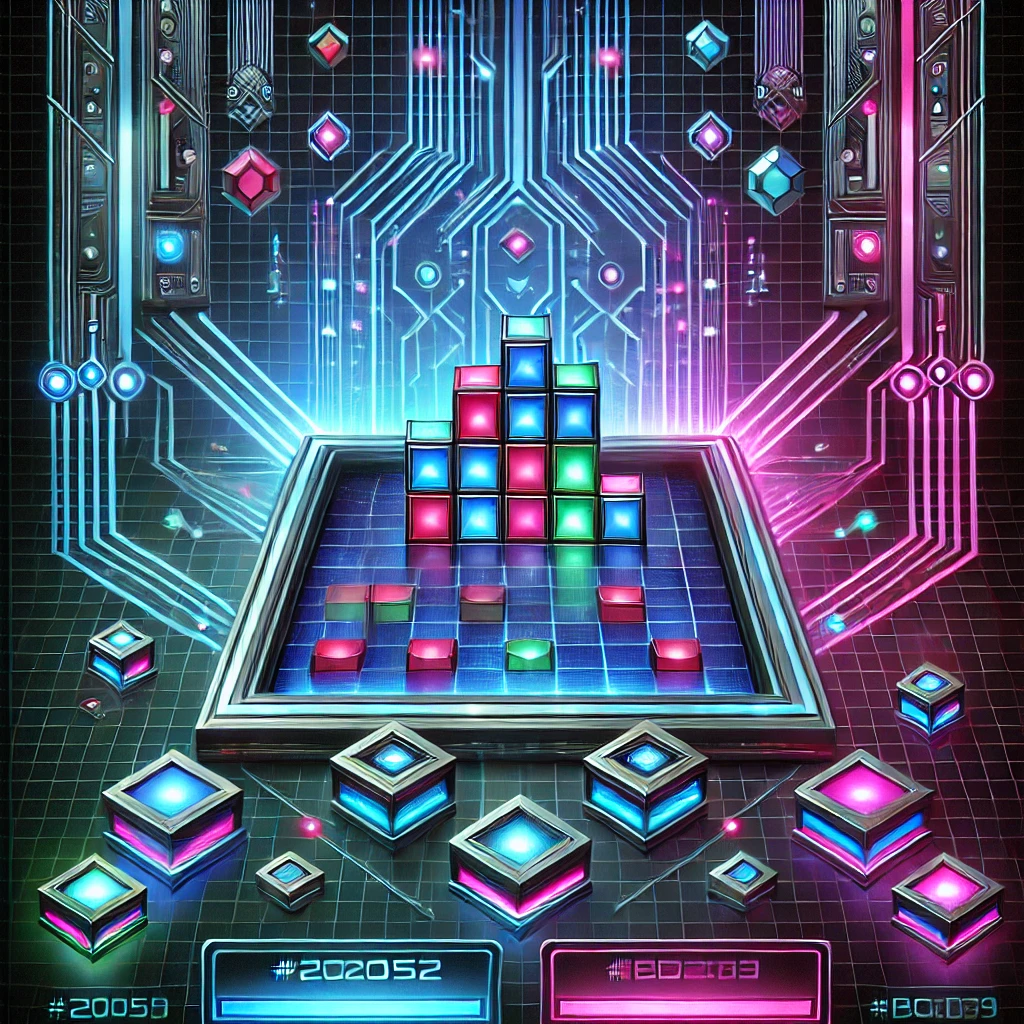
Industry 4.0 and IoT
Client Overview
A large-scale manufacturing company with four production facilities, operating numerous complex machines, aimed to enhance operational efficiency and reduce downtime through real-time monitoring, analytics, and improved maintenance practices. They sought to leverage IoT and Industry 4.0 capabilities to gain comprehensive insights into their machine operations.
Challenge
The manufacturer faced several challenges:
- Lack of Real-Time Visibility: Limited access to real-time data on machine performance, leading to reactive maintenance and unplanned downtime.
- Inefficient Communication: Difficulty in disseminating critical information to leaders, stakeholders, maintenance technicians, and managers.
- Data Silos: Disparate data sources and systems, hindering comprehensive analysis and decision-making.
- Proactive Maintenance Issues: The companies maintenance was mostly reactive instead of proactive.
- Parts Stocking Inefficiencies: Frequent unavailability of necessary spare parts, leading to prolonged machine downtime.
- Unstructured Maintenance Schedules: Lack of standardized maintenance codes and tracking, making it difficult to analyze maintenance trends and optimize schedules.
Solution
Tetra Labs developed and implemented an IoT-enabled machine monitoring and analytics platform that:
- Deployed IoT sensors to collect real-time data on machine performance.
- Developed a centralized data platform to aggregate and process data from various sources.
- Created customizable dashboards and visualizations to provide real-time insights.
- Implemented a notification system to alert personnel to critical events.
- Implemented a structured maintenance tracking system with standardized codes for machines and maintenance types.
- Integrated parts inventory tracking with the maintenance system to optimize spare parts stocking and consumption.
Results
Quantifiable Outcomes:
- Reduced Downtime: The real-time monitoring and analytics platform reduced machine downtime by 15%.
- 10% of this reduction was directly attributable to improved parts stocking and structured maintenance schedules.
- Increased production: Due to the reduced downtime, the company saw a 7% increase in overall production.
- Reduced maintenance costs: The proactive notifications and dashboards reduced maintenance costs by 20% due to less emergency repairs and expedited shipping costs for spare parts.
- Improved response time: The notification system reduced the response time to critical events by 40%.
- Reduced part related down time: The new parts tracking and maintenance schedule reduced part related down time by 100%.
Qualitative Outcomes:
- Enhanced Visibility: Real-time dashboards provided comprehensive insights into machine operations.
- Improved collaboration: The platform facilitated seamless communication.
- Data-Driven Decision-Making: The availability of real-time data and analytics empowered the client.
- Proactive Maintenance: The predictive analytics and real time notifications allowed for a shift to proactive maintenance.
- Increased Stakeholder satisfaction: All stakeholders had access to real time data, and felt more informed.
- Optimized Parts Inventory: The integration of parts inventory tracking improved spare parts availability.
- Structured Maintenance: Standardized maintenance codes and tracking enabled better analysis of maintenance trends.
Conclusion
Tetra Labs' IoT-enabled machine monitoring and analytics platform, with the added benefit of structured maintenance schedules and improved parts stocking, significantly improved the manufacturer's operations. By providing real-time insights, facilitating communication, enabling proactive maintenance, and optimizing spare parts availability, the client was able to reduce downtime, increase production, and optimize overall efficiency. This case study further underscores the transformative power of IoT and Industry 4.0 technologies in the manufacturing sector.