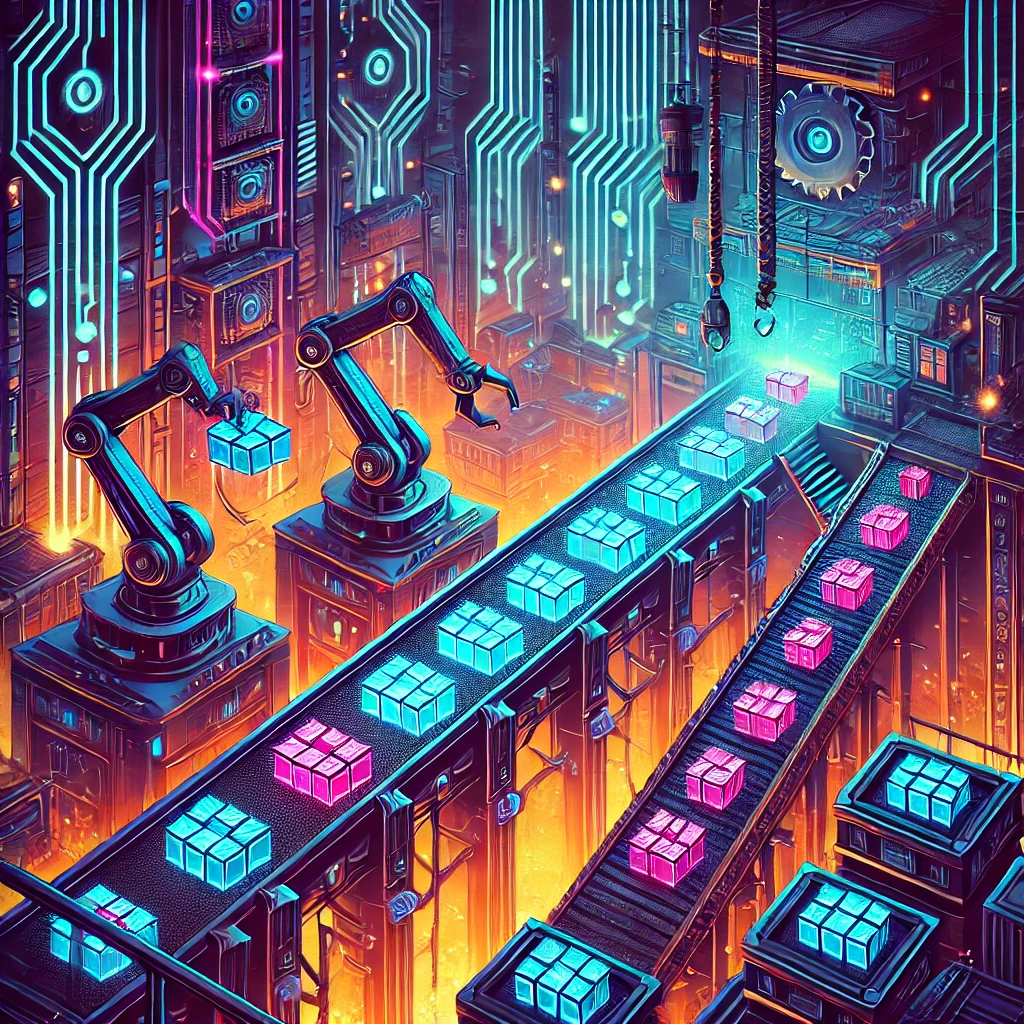
Supply Chain Optimization
Client Overview
A large manufacturing company, generating $200 million in annual revenue, faced significant challenges in its supply chain, including order processing delays, frequent stockouts, and high warehouse storage costs. They sought to automate and optimize their supply chain to improve efficiency and reduce costs.
Challenge
The manufacturer experienced several critical challenges:
- Manual Order Processing: Manual order processing led to delays and errors, impacting production schedules and customer satisfaction.
- Stockout Issues: Inaccurate demand forecasting resulted in frequent stockouts, causing production delays and lost sales.
- High Warehouse Costs: Inefficient inventory management led to excessive warehouse storage costs and wasted space.
- Lack of Real-Time Visibility: Limited visibility into the supply chain made it difficult to identify and address bottlenecks.
- Delays: Delays in getting required parts, caused production delays, and increased costs.
Solution
Tetra Labs developed and implemented a comprehensive supply chain automation and optimization solution that:
- Automated order processing using AI and machine learning algorithms.
- Implemented real-time demand forecasting and inventory management.
- Integrated with suppliers and logistics providers for seamless communication and tracking.
- Developed a centralized dashboard for real-time supply chain visibility.
- Created an automated parts order system, that would automatically order parts when stock reached a specific level.
- Optimized warehouse space utilization through intelligent storage and retrieval systems.
Results
Quantifiable Outcomes:
- Reduced Order Processing Time: Automated order processing reduced processing time by 50%, saving approximately $100,000 annually in administrative costs.
- Reduced Stockouts: Improved demand forecasting and inventory management reduced stockouts by 30%, resulting in an estimated $2 million increase in annual revenue.
- Reduced Warehouse Costs: Optimized warehouse space utilization and inventory management reduced warehouse storage costs by 20%, saving approximately $500,000 annually.
- Reduced Delays: Automated parts orders and better real time updates, reduced delays by 40%. This equated to roughly 800,000 dollars in saved costs, due to reduced production delays.
- Improved Inventory Accuracy: Inventory accuracy increased by 95% due to the new system.
Qualitative Outcomes:
- Improved Customer Satisfaction: Faster order processing and reduced stockouts led to improved customer satisfaction.
- Enhanced Supply Chain Visibility: Real-time dashboards provided comprehensive visibility into the supply chain, enabling proactive decision-making.
- Increased Efficiency: Automation and optimization streamlined supply chain processes, improving overall efficiency.
- Reduced Operational Costs: The system reduced operational costs, and increased revenue.
- Improved Supplier Relationships: Real time data sharing, improved communication with suppliers.
Conclusion
Tetra Labs' supply chain automation and optimization solution significantly improved the manufacturer's operational efficiency and reduced costs. By automating order processing, optimizing inventory management, and providing real-time visibility, the client was able to reduce stockouts, lower warehouse costs, and improve customer satisfaction. This case study demonstrates the transformative impact of digital solutions in optimizing complex supply chain operations.